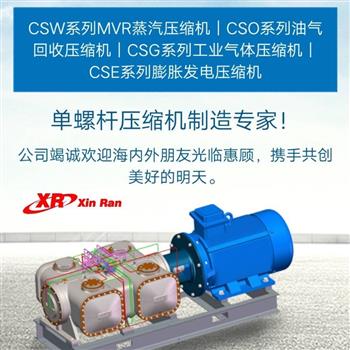
下列标准均按最新版执行
压缩机标准: |
|
参照 API-619 |
一般炼油厂装置用旋转式正位移压缩机; |
API-614 |
专用的润滑、轴密封和控制油系统; |
API-671 |
炼油厂特殊用途联轴器 |
GB/T25357 |
石油、石化及天然气工业流程用容积式回转压缩机; |
SH/T 3157 |
化工回转压缩机工程技术规定 |
电机及电气标准: |
|
GB755 |
旋转电机定额和性能; |
GB3836.1-2010 |
爆炸性气体环境用电气设备 第1部分:通用要求; |
GB3836.2-2010 |
爆炸性气体环境用电气设备 第2部分:隔爆型“d”; |
GB3836.3-2010 |
爆炸性气体环境用电气设备 第3部分:增安型“e”; |
GB3836.4-2010 |
爆炸性气体环境用电气设备 第4部分:本质安全型“i”; |
管道与阀门标准: |
|
SH3406 |
石油化工钢制管法兰(对外接口) |
SH3059-2001 |
石油化工管道设计器材选用通则 |
GB9948-2006 |
石油裂化用无缝钢管 |
GB/T8163-2008 |
输送流体用无缝钢管 |
法兰面密封形式 |
RF |
垫片 |
柔性石墨缠绕式垫片06Cr19Ni10(注:法兰的密封面与其连接的阀门或设备管嘴的密封面相匹配;法兰的接口外径与壁厚应与其对接的管道的外径与壁厚相一致。) |
自控仪表标准: |
|
API670-2003 |
非接触式轴振动,轴位移测量系统 |
SH/T3019-2003 |
石油化工仪表管道线路设计规范 |
GB50093-2002 |
工业自动化仪表工程施工及验收规范 |
环境保护标准: |
|
SH3024 |
石油化工企业环境保护设计规范 |
GBZ 2.2-2007 |
工作场所有害因素职业接触限值 第2部分:物理因素 |
GBZT189.8-2007 |
工作场所物理因素测量噪声 |
压力容器标准: |
|
GB150~150.4-2011 |
钢制压力容器 |
GB151-1999 |
管壳式换热器 |
TSGR0004 |
固定压力容器安全技术监察规程 |
JB4730 |
压力容器无损检测 |
1.2 优先原则
如果下面的文件发生冲突,其优先的顺序应是:
a. 技术协议
b. 数据表
c. 用户前期提供至供货商文件
d. API-619 标准及与其相关的规范标准
当所列标准发生冲突时,按较严格标准执行。
2.0 技术要求
2.1螺杆压缩机
2.1.1 操作参数(单台套):
项目 |
单位 |
工况 |
介质 |
|
工艺气 |
入口温度 |
℃ |
<50 |
进口流量 |
Nm3/h |
1500 |
进口压力 |
kPa(G) |
2 |
出口压力 |
MPa(G) |
0.55 |
出口温度 |
℃ |
<60 |
分子量 |
|
29.6 |
2.1.2 气体组分:
气体成分:MOL% |
分子量 |
主工况 |
CO |
28 |
60-70 |
CO2 |
44 |
15-20 |
O2 |
32 |
0.3-0.5 |
H2 |
2 |
2-6 |
N2 |
34 |
7-10 |
H2O |
18 |
饱和 |
杂质 |
|
|
2.2螺杆压缩机
2.2.1 信然工艺气体压缩机采用单螺杆式,信然单螺杆工艺气体压缩机的设计和制造参照执行API-619标准。
2.2.2 生产厂商负有机组及辅助设备、系统的总成套设计、制造、性能、检验、试验、质量、供货、服务等责任。信然压缩机的设计寿命为20年,试验阶段不间断连续运行时间至少1年。
2.2.3 信然单螺杆压缩机、驱动电机及其它设备在规定环境条件下启动和连续操作,在全部工艺工况下达到预期性能。且具备结构合理、选材适当、动力平衡性能良好、振动小、噪音低、密封可靠、易损件寿命长等特点。
2.2.4 信然单螺杆压缩机组安装在室内,撬装,采用单层结构,压缩机及辅助设备布置应便于安装检修,同时给操作人员巡检提供足够的通道和空间,重要的密封面应带有配合标记。
2.2.5 所有的电气设备、电气元件、仪表和其它仪电材料的选择,以及它们的安装都应满足压缩机数据表规定的电气危险场所分类及现场环境条件的要求。
2.2.6 信然单螺杆压缩机为单级压缩,由异步隔爆变频电动机驱动。压缩机为单螺杆结构,由螺杆带动星轮转动。
2.2.7 信然压缩机轴封系统采用双端面机械密封,一螺杆轴上两个,两星轮轴上各一个,隔离液采用除盐水。
2.2.8 信然单螺杆压缩机内部采用喷除盐水冷却工艺,保证出口温度<45℃,保证机组能长周期安全运行。
2.2.9 信然压缩机螺杆轴两端采用滚动轴承,星轮轴一端采用滚动轴承,另一端径向轴承均采用滑动轴承。滚动轴承每个轴承设插入式测温计,温度计现场显示。
2.2.10 信然压缩机壳体为整体铸造,能适应较高排气压力和带液操作工况,壳体密封面与介质气接触面积小,可以满足介质气零泄漏的苛刻工况,适用于工艺气等易燃易爆剧毒气体。压缩机进、出口型式采用上进下出。冷却液体随气体一同排出,压缩机组设计考虑压缩机内部不积液。
注:压缩机进出口规格:
|
口径 |
压力等级 |
密封面 |
接管壁厚等级 |
法兰材质 |
入口 |
DN150 |
CL150 |
RF |
Sch20 |
304 |
出口 |
DN100 |
CL150 |
RF |
Sch20 |
304 |
2.2.11 螺杆星轮啮合其型线的设计要充分考虑吸入条件(压力、组分、杂质等)大范围波动时,转子所能承受的交变应力。
2.2.12 信然压缩机壳体材料采用奥氏体不锈钢材质。
2.2.13 信然压缩机、驱动机采用刚性重型联合底座(联合底座应有足够的刚性1:1000,能够现场整体吊装)。在电机底脚处应设横向、轴向调位螺钉,底座周边设调水平顶丝。底座带有接地端子,采用M24×300地脚螺栓,由供货商配套。
2.2.15 信然压缩机出入口管口允许受力和力矩应满足API-619最新标准规定值的1.5倍。
2.2.16 信然压缩机设有回流卸压阀组,该阀组安装在内部工艺管线,回流至压缩机入口。
2.2.17 供货商提供机组底座范围内的所有工艺管线、喷液管线、密封油管线、气控管线等。这些管线尽量分类集合成一个接头接到底座边缘,以法兰形式同用户管线相连接,供货商提供配对法兰、双头螺栓。底座范围内的所有管线在供货商厂房安装好,所有与用户连接的对外接口法兰标准采用ASME B16.5 150LB RF。
2.2.18 冷却水系统法兰选用CL150,水侧最大压降≯0.1Mpa,冷却设备水侧温升≤10℃,管件、阀门采用碳钢。
2.2.19 压力容器按照GB150标准设计。
2.2.20 压缩机主要技术参数
机组型号 |
XRGY25/0.02-5.5 |
|
吸气量(入口状态) |
1500Nm³/H |
|
吸入压力/吸入温度 |
2 kPa(G)/ 常温 |
|
排气压力/排气温度 |
0.55MPa(G)/60℃ |
|
转子直径 |
310mm |
|
星轮直径 |
310mm |
|
轴功率 |
160.4kW |
|
机组转速 |
2980rpm |
|
径向轴承型式 |
滚动轴承 |
|
轴封形式 |
机械密封 |
|
材料 |
壳体 |
316 |
螺杆 |
316 |
|
星轮片 |
PEEK+30%碳纤维 |
|
流量调节方式 |
旁路回流调节 |
2.3 主电机和附属设备
2.3.1 主电机采用一台防爆型变频低压异步电机(3Ph,380V,50Hz),防爆等级EX dIICT4,外壳和接线盒的防护等级IP55,绝缘等级为F级,按照B级温升考核。
2.3.2 起动及运行要求
2.3.2.1 全压空载变频起动,起动次数允许冷态两次,热态一次。
2.3.2.2 电机起动时,电机端电压不小于额定电压的80%。
2.3.2.3 当电源电压与额定电压偏差不超过±10%,电动机输出功率应连续保持为额定值,此时温升按B级(绝缘等级为F级时)考核,电动机最高表面温度不超过T4组别温度要求。
2.3.2.4 当电源频率与额定频率的偏差不超过±2%时,电源电压与额定电压的偏差不超过±5%时,或电压和频率同时出现极限偏差时,电机输出功率应连续保持额定值,此时,温升按B级(绝缘等级为F级)考核。
2.3.2.5 当电源电压与额定电压的偏差不超过+l0%~+5%,-10%~-5%或当电源频率与额定频率的偏差不超过+5%、+2%、-5%、-2%;或者当电源与频率同时出现偏差时,电机榆出功率应连续保持为额定值,此时,温升按F级(绝缘等级为F级时)考核,且电动机最高表面温度不超过T4组别的温度要求。
2.3.2.6 正常运行时,当电源电压下降到额定电压的85%时,电动机应在额定功率下连续运转10S,且电动机最高表面温度不超过T4组别的温度要求。
2.3.2.7 在以上正常操作条件下电机应无火花、无电弧,并且任何部位的表面温度都不超过T4组别的温度要求。
2.3.3 电动机的结构与安装方式
2.3.3.1 电动机应符合国家隔爆型电机标准GB3836-2010,防爆等级dIICT4。
2.3.3.2 电动机为卧式安装,双轴承支撑。每个轴承设插入式测温表。
2.3.3.3 电动机冷却方式为空冷。
2.3.3.4 电机轴承选型为滚动轴承,润滑方式为脂润滑。
2.3.4 电动机壳内装有防潮空间加热器,电压为220VAC、单相,加热器设独立的接线盒,与主接线盒同侧,进线方式为铠装电缆。
2.3.6 电动机上所有标牌牢固的固定在静止部件上,安装位置明显并容易观察。所有标牌材料均为不锈钢材料。
2.3.7 主接线盒的绝缘子使用复合绝缘子,不允许使用陶瓷绝缘子。户外电动机的接线盒配防雨罩。
2.3.8 电机制造厂应对该电机进行出厂试验和型式试验,试验方法及内容严格按GB/T1032、GB3836.3的规定。
2.3.9 电动机的额定功率须按满足连续运行的条件下,负载所需的轴功率来选择,并且还要考虑储备系数和温度修正系数,一般取大于或等于1.1倍的所驱动负载的轴功率,且不小于出口安全阀定压下的功率计算值。
2.3.10 主电机技术参数如下:
电压/功率/转速:380V/200KW/2980rpm
防爆等级/防护等级:EX eIICT4/IP55
电机绝缘等级F级,温升按B级考核。
项目 |
技术参数 |
备注 |
额定功率(KW) |
200 |
滚动轴承 油脂润滑 |
额定电压(V) |
380 |
|
同步转速(r/min) |
2980 |
|
相数 |
3 |
|
频率 |
20-50HZ |
|
极数 |
2 |
2.3.11油泵电机技术参数如下:
电压/功率/转速:380V/1.5KW/1500rpm
防爆等级/防护等级:EX dIICT4/ IP55
项目 |
技术参数 |
备注 |
额定功率(KW) |
1.5 |
滚动轴承 油脂润滑 |
额定电压(V) |
380 |
|
同步转速(r/min) |
1450 |
|
相数 |
3 |
|
极数 |
4 |
2.3.12机组主电机、油泵电机等各马达所需的起停操作由购买方提供启动柜控制,机组主电机与启动柜的动力连接电缆由购买方提供。
3.4联轴器和防护罩
3.4.1信然压缩机与主电机之间的联轴器为弹性膜片式联轴器。
3.4.2所有可能危及人身安全的运动部件均提供防护罩,防护罩由全封闭、无火花、铝合金材料制造。
3.4.3 联轴器使用系数至少1.75。
3.5密封油系统plan54
3.5.1 plan54系统设计和制造参照执行API-614最新版的标准
3.5.2 plan54系统包括以下主要设备
l 一台不锈钢油箱;
l 两台油泵,互为备用;
l 一台油冷却器(管壳式);
l 一台双联式油过滤器,带有恒流量转换阀,过滤芯精度为10μm;
l 一台自力式压力控制阀,用以控制维持供油总管压力稳定
l 一套供油和回油管线系统;
l 所有必需的仪表。
3.5.3 主、辅油泵具有机组所需要的油量的120%的容积流量。两台油泵均互为主辅。
3.5.4 主、辅油泵均采用电机驱动,驱动机防爆等级:dⅡCT4;防护等级:IP55。
3.5.5 油冷却器采用管壳式冷却器,油冷却器的设计和制造应符合GB151的规定。油冷却器管束采用不锈钢材质,壳体为碳钢。水侧的最大压降不超过0.07Mpa,水走管程,隔离液走壳程。冷却器的设计按120%的流量考虑。
3.5.6 双联过滤器过滤器具有150%容积流量。油过滤器滤芯材质为不锈钢,滤芯起始压差不大于0.03MPa(G)。能够在不停机的情况下完成过滤器的切换及清洗。
3.5.7 油箱至少应该有5分钟的滞留时间和3分钟的工作时间。回油系统的大小能容纳两台油泵同时工作的全负荷流量。
3.5.8 隔离液油系统所有管线和管件材料均是不锈钢,管子为无缝钢管。所有油路系统采用亚弧焊打底,并进行酸洗钝化处理。
3.5.9 油箱上装有液位计、温度计、以及排凝阀,其中液位计上应标明最高及最低操作液位,油箱设置低位排液。
3.5.10 隔离液油系统管线上设有管路高点放空和低点排凝。
3.5.11 各供油点回油管线上设有视镜。
3.5.12 密封液油系统供油管线给压缩机机械密封供油,管路上设置油压就地显示、低报警、调节。
3.5.13 密封油采用15#白油。
3.6 喷液冷却系统
3.6.1 压缩机采用除盐水喷淋冷却,喷液冷却系统包括喷液控制阀组和喷液过滤器、冷却器、气液分离器等。
3.6.2 气液分离器上设有液位变送器,压力表和温度计,自动排液阀。气液分离器里设有旋风分离导流板。气液分离器的设计和制造应符合GB150规范。气液分离器壳体采用304不锈钢。气液分离器的容量足够保证压缩机系统的内部喷液循环顺利完成。
3.6.3 液液冷却器的结构无需拆卸工艺管线就能抽出管束,除盐水走壳程,冷却水走管程。冷却水下进上出,冷却水侧温升不低于8℃。壳体管束均采用304不锈钢。
3.6.4 喷液过滤器为双联式,过滤器过滤精度为10μm,并带有手动切换阀,能够在不停机的情况下完成过滤器的切换及清洗。
3.7 仪表控制系统
3.7.1 所有仪表均用SI单位,压力单位MPa,温度℃。
3.7.2 机组所有变送器为本安型,防爆等级为iaIICT4,防护IP65,4-20mA,带数字表头;热电阻的防爆等级为dIICT4, 防护IP65;
3.7.3 供货商提供现场一次仪表,包括现场压力变送器、热电阻、液位变送器、压力表、差压表、温度计、液位计等,各测控点详见仪表带控点流程图,要求在测量表上挂带钢印的不锈钢牌。
3.7.4 所有开关量仪表的触点容量应为220VAC,5A。
3.7.5 所有压缩机橇内的一次仪表接线至现场防爆接线箱,防爆接线箱防爆等级为ExdIICT4,防护IP55,接线箱安装在橇装边缘。本安信号和隔爆信号、模拟量和数字量均分别接不同的接线端子。一次仪表至接线箱的电缆为1.5mm2阻燃型屏蔽电缆,在压缩机橇内走桥架槽盒,槽盒接地间隔20米,电缆的两端做标识牌,分别注明信号来源和端子号。注意需完善现场保护地和室内信号地。所有信号进现有机柜间控制系统,由供货商提供控制方案,通过控制系统实现机组的控制和状态监测。购买方提供主电机变频柜,置于安全区域。
3.7.6 现场接线箱面板设置压缩机操作按钮和主电机电流表,强弱电须分别设置独立的接线箱,互不干涉,接线箱接地引至箱外。
3.7.8 压缩机控制逻辑方案由供货商提供,由购买方的DCS厂家对逻辑图进行标准化转换。
a) 压力(差压)
检测项目 |
就地 |
仪表架 |
DCS |
||
显示 |
显示 |
显示 |
报警 |
联锁停车 |
|
压缩机进气压力 |
√ |
|
√ |
√(L) |
|
压缩机排气压力 |
√ |
|
√ |
√(H、HH) |
√(HH) |
压缩机喷液压力 |
√ |
|
√ |
√(L、LL) |
|
密封油系统压力 |
√ |
|
√ |
√(L) |
|
密封油系统过滤器压差 |
√ |
|
|
|
|
循环喷液过滤器压差 |
√ |
|
|
|
|
进气过滤器压差 |
√ |
|
|
|
|
仪表风控制气压力 |
√ |
|
|
|
|
各密封油回油点压力 |
√ |
|
|
|
|
b) 温度
检测项目 |
就地 |
仪表架 |
DCS |
||
显示 |
显示 |
显示 |
报警 |
联锁停车 |
|
压缩机排气温度 |
√ |
|
√ |
√(H) |
|
密封油油箱温度 |
√ |
|
|
|
|
压缩机轴承温度 |
√ |
|
|
|
|
主电机轴承温度 |
√ |
|
|
|
|
循环喷液温度 |
√ |
|
|
|
|
c) 液位
检测项目 |
就地 |
仪表架 |
DCS |
||
显示 |
显示 |
显示 |
报警 |
联锁停车 |
|
压缩机主机液位开关 |
|
|
√ |
√ |
√(开机联锁) |
密封油箱液位 |
√ |
|
√ |
√(L) |
|
气液分离器液位 |
√ |
|
√ |
√(H L) |
|
d) 启动条件
项目 |
要求 |
备注 |
密封油系统 |
油泵运行,油压大于最小值 |
|
压缩机主机液位开关 |
无报警 |
|
压缩机入口阀 |
关闭 |
|
压缩机喷液阀 |
关闭 |
|
4.0 检验与试验
4.1 检 验
4.1.1 对压缩机的主要零件如:壳体、螺杆、星轮,进行材料的机械性能或化学成分分析,并出具报告。
4.1.2 对压缩机耐压件作静压试验,结果应符合相关技术要求。
4.1.3 压缩机的无损探伤项目:
零件名称 |
磁粉 MT |
着色 PT |
超声波 UT |
射线 RT |
壳体 |
|
Y |
|
|
轴 |
|
Y |
Y |
|
螺杆 |
|
Y |
Y |
|
4.2 试验
4.2.1 机组开发完成整体组装后,在制造厂做原速(操作转速)出厂试验,内容如下:
|
见证试验 |
非见证试验 |
备注 |
水压试验 |
|
Y |
|
机械运转试验 |
Y |
|
|
4.2.2 对上述见证试验,供货商应提前10天书面通知购买方派人参加,如逾期不来人员时,按原计划进行下一道工序。
4.2.3 合同电机出厂前在电机厂应单独进行机械运转试验, 压缩机和电机机械运转试验、压缩机性能试验至少为10小时。
4.2.4 机组在制造厂进行机械试运转时,要求使用合同压缩机、合同电机、合同联轴器、合同密封、合同轴承,所有性能满足协议中相关标准要求,经购买方确认合格签字后方能出厂。
4.2.5 性能试验时达到如下要求:
项目 |
单位 |
技术指标 |
压缩机排气量 |
m³/min |
≮25×95% |
压缩机排气压力 |
MPaG |
≮0.55 |
轴功率 |
KW |
≯额定功率×104%(空气介质) |
压缩机轴承温度 |
℃ |
≯85 |
电机轴承温度 |
℃ |
≯95 |
振动 |
mm/s |
≯8 |
噪音 |
dB |
≯85(电机、调压阀除外) |
5.0制造监理和节点设置
对约定的购买方参与的见证点、停止点,购买方认为其制造过程达到控制节点并在其质量保证体系运行正常时提前7天书面通知购买方。若购买方因故无法赴制造厂则视为自动放弃。
5.0 图纸资料交付
设计图纸、技术文件和手册清单具体如下:
1 合同生效后4周内提供给购买方4份中间审查资料,并提供电子版。提交图纸后2周内,由购买方负责召开技术协调会,具体日期及地点双方商定。 2协调会后2周提供的最终资料,电子版各一份。 3 装订成册的随机资料4份,包含所有压力容器资料。并提供电子版。 |
||||
序号 |
资料名称 |
1 |
2 |
3 |
1 |
机组总布置图 |
√ |
√ |
√ |
2 |
压缩机数据表 |
√ |
√ |
√ |
3 |
压缩机总装配图 |
√ |
√ |
√ |
4 |
基础条件图 |
√ |
√ |
√ |
5 |
机组重心图 |
√ |
√ |
√ |
6 |
气路系统PID图 |
√ |
√ |
√ |
7 7 |
冲洗系统PID图 |
√ |
√ |
√ |
8 |
喷液系统PID图 |
√ |
√ |
√ |
9 |
测温系统流程图 |
√ |
√ |
√ |
10 |
机组报警、联锁逻辑框图、联锁逻辑图及说明 |
√ |
√ |
√ |
11 |
报警及联锁一览表 |
√ |
√ |
√ |
12 |
仪表设备规格表 |
√ |
√ |
√ |
13 |
接线端子图 |
√ |
√ |
√ |
14 |
电动机外形图(含端子箱接线图及接线箱) |
√ |
√ |
√ |
15 |
气体出口单向阀、入口过滤缓冲罐规格尺寸 |
√ |
√ |
√ |
16 |
气液分离器单体图 |
√ |
√ |
√ |
17 |
冷却器单体图 |
√ |
√ |
√ |
18 |
机组水、电、气消耗指标分列及汇总表 |
√ |
√ |
√ |
19 |
压缩机出厂试验检验报告 |
|
|
√ |
20 |
机组安装、维护及操作使用说明书 |
|
|
√ |
21 |
机组产品合格证 |
|
|
√ |
22 |
装箱清单 |
|
|
√ |
23 |
所有分供设备的合格证书及说明书(按分供厂家数量提供) |
|
|
√ |
24 |
其它常规的出厂随机资料 |
|
|
√ |
6.0 性能保证
6.1 现场的性能试验应以现场的实际介质进行;机械运转、性能试验、振动都应满足要求;购买方应派出代表参加现场考核与验收。
6.2 性能保证(正常工况):
6.2.1 压缩机轴功率:偏差不大于+4%
6.2.2 压缩机排量:≥95%
6.2.3 压缩机排气压力: 无负偏差
6.2.5 机械密封寿命: 8000h
6.3 机组在正常操作条件下无故障连续运行时间至少为8000小时。
6.4 在保证期内,供货商应保证免费更换因产品质量问题而发生故障的或有缺陷的部件。更换部件质保期为自更换日期开始起一年。
6.5 噪音离机组一米不超过85dBA(电机除外)。
6.6 设备质保期为设备开车后12个月,或设备到现场18个月内,以先到日期为准。
6.7 压缩机设计寿命20年以上。
7.0 服务承诺
7.1 供货商提供工艺气单螺杆压缩机组一台套,保证成套压缩机设备的完整性,单台套机组的范围如下 (与PID互为补充):
序号 |
设备名称 |
设备型号 |
数量 |
备注 |
1 |
单级无油喷水单螺杆式工艺气压缩机 |
XRGY25 |
1台 |
|
2 |
叠片式联轴器带无火花型全封闭防护罩 |
|
1套 |
|
3 |
低压防爆主电机 |
200KW |
1台 |
|
4 |
密封辅助系统 |
PLAN54系统 |
2套/台 |
|
5 |
压缩机循环喷液冷却系统 |
|
1套 |
带液液冷却器、双联过滤器、控制阀组等 |
6 |
气液分离器 |
|
1台 |
带液位仪表、自动排液、补液控制阀组 |
7 |
重载型钢焊接联合底座(压缩机、电机、管路系统共用) |
|
1套 |
包括地脚螺栓、螺母、调整顶丝、起吊环 |
8 |
压缩机入口开关阀 |
|
1台 |
|
9 |
压缩机入口过滤器 |
|
1台 |
|
10 |
压缩机出口最小压力阀 |
|
1台 |
|
11 |
气液分离罐安全阀 |
|
1套 |
|
12 |
回流卸荷阀 |
|
1套 |
|
13 |
机组就地一次仪表(底座范围内)、仪表架、电缆及安装材料(以接线盒出线端子为界) |
|
1套 |
|
14 |
就地接线箱,操作柱 |
|
1套 |
|
15 |
底座范围内的管路 |
|
1套 |
|
16 |
所有与用户连接的法兰及对应法兰、螺栓、螺母、垫片等 |
|
1套 |
|
7.2 供货商向购买方提供备件应包括:
序号 |
名称 |
数量 |
1 |
压缩机 |
|
1.1 |
滚动轴承 |
100% |
1.2 |
各规格O型圈 |
100% |
2 |
辅助系统(plan54、喷液系统) |
|
2.1 |
双联过滤器芯 |
100% |
2.2 |
喷液过滤器芯 |
100% |
注:100%指一台套机组所配置数量
7.3 供货商对提供的所有设备的安装、开车、检查提供免费技术指导。
7.4 供货商派遣经过专业培训并具有丰富经验的人员赴购买方处进行现场服务。并向购买方提供预定人员的简历以征得购买方认可。购买方有权否决供货商所派人员,指定替换人员。
7.5 供货商有责任赔偿由于服务人员履行职责期间疏忽大意而造成人员及设备的损失费用。
7.6 机组在现场投入运行后,供货商将对产品的质量状态进行跟踪并提供及时周到的售后服务。在接到购买方于质量问题的电话或传真件后12小时内对购买方提出的问题给予答复(电话或传真)。如需要去现场解决问题,则于24小时内派人赴现场处理问题,直到问题解决。
7.7 在合同规定的质保期内,因供货商原因造成产品损坏,应由供货商负全责。
8.0 油漆、标志、包装和运输
8.1 油漆
除非另有说明,除机加工表面外,所有铁素体材料的外表面应涂至少两层底漆和一层面漆,在加工的外表面应全部涂以防锈剂。油漆颜色协调会定;
8.2 铭牌和转向箭头
8.2.1 铭牌应牢固地固定在设备上和任何其他辅助设备的主要部件上醒目的位置,所有可拆卸的部件应有相应的配合标记;设备应标识上位号和序列号。单独发运的材料应牢固地钉上耐腐蚀的金属标牌,标牌上指明预定采用压缩机的位号和序列号。装箱的设备发货时应附带两份装箱单,一份放在包装箱内,另一份放在包装箱的外面。
8.2.2 压缩机组、驱动机、辅助转动机器的铭牌和转向箭头采用不锈钢材料制造,以下数据被清楚的标记在铭牌上。
1)机组
包括制造单位、设备位号及设备名称、机器型号和规格、制造系列号、出厂编号、额定流量和额定压力、转数、制造日期。
2)其他辅助装置
包括制造单位名称、系列号、型号及规格、出厂编号、制造日期。
8.2.3 设备的序列号除了打印在铭牌上外,还应清晰永久地标志在机壳上。
8.2.4 转向箭头应铸在或固定在旋转设备每个主要部件的醒目地方。
8.3 包装和运输
8.3.1 供货商应按设备及其辅机将在现场没有任何保护的情况下储存至少6个月考虑,机组的内表面涂一层与润滑油相容的溶性油防锈剂。暴露的轴和联轴器应用防水的塑料涂蜡织物或气相腐蚀抑制剂纸包裹。接缝处应用防油胶带密封住。对所有零部件进行清洁、防锈和妥善的保护处理。
8.3.2 所有的开口法兰开口配置一个至少2~3mm厚的金属板,并带有橡胶垫片和至少4个配该法兰螺栓孔直径的螺栓。所有螺纹孔应用塞子封堵,所有设备和材料都应妥善包装,可靠固定,以防运输过程中损坏。
8.3.3 压缩机组的装运工作应在检查和试验验收合格后,并经过购买方同意,方可进行。
8.3.4 起吊点和吊耳应清楚地标明。
8.3.5 所有随机配件需单独包装,并标识清楚;供货商对运输过程负全责。
8.3.6 每个包装箱,需有二份装箱单,一份在箱子外,一份在箱子内,外面的需有防湿措施。
更多详情请登陆:www.xinrancompressor.cn
电 话:13621769700 18621809999